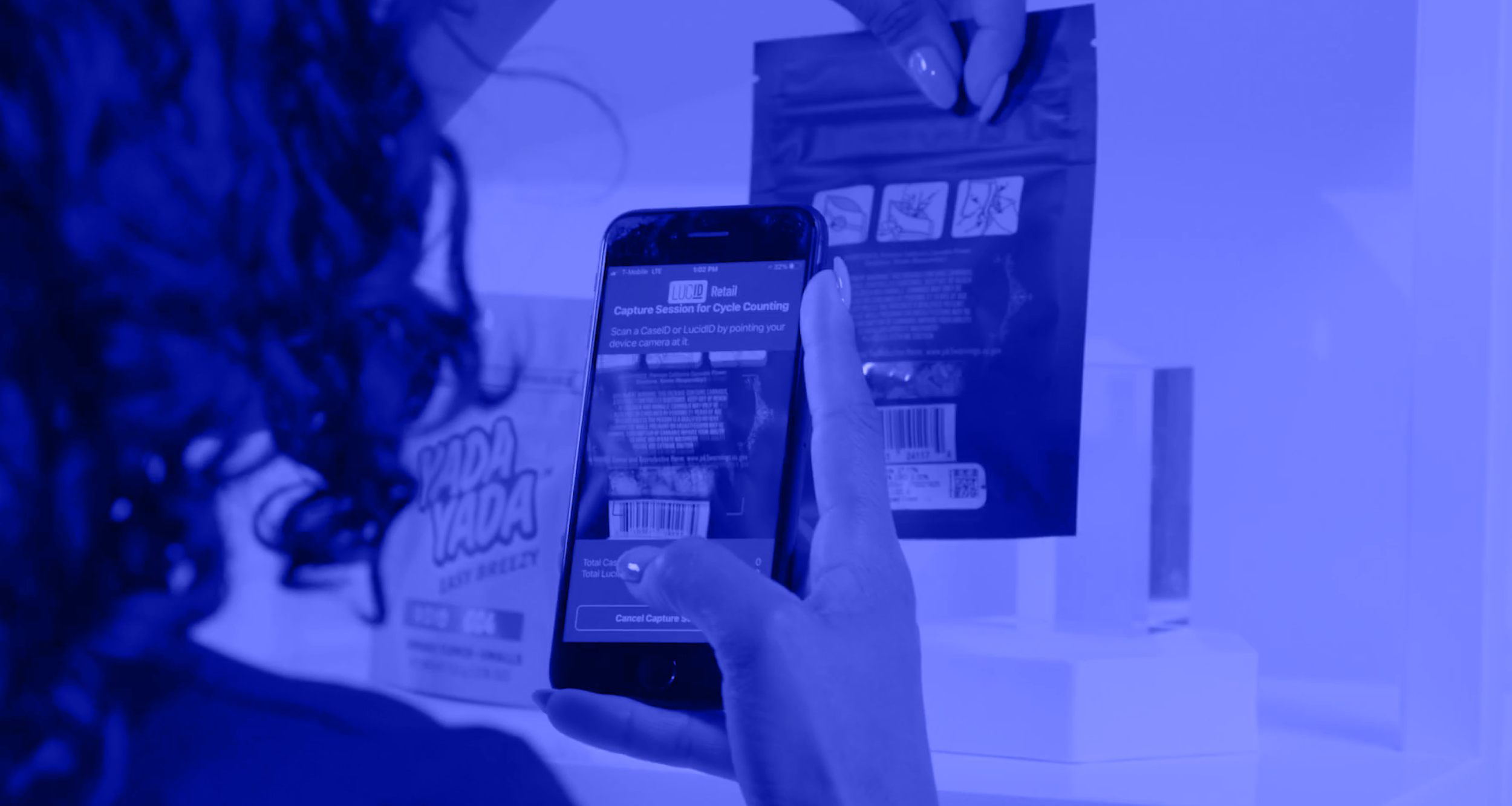
A Seamless Cannabis Inventory Management Solution to Optimize Your Supply Chain
Stickering and cannabis inventory management is a major challenge. We all feel it. All our supply chain processes are shaped by it. The way we identify products in the cannabis industry affects our costs, timelines, and overall growth opportunities.
The stickering process is not standardized when it comes to cannabis supply chain management. That should be no surprise to anyone. But we are here to help enable the cannabis industry to work smart.
Pause for a moment and explore retailers who accept LucidID’s to efficiently manage their inventory
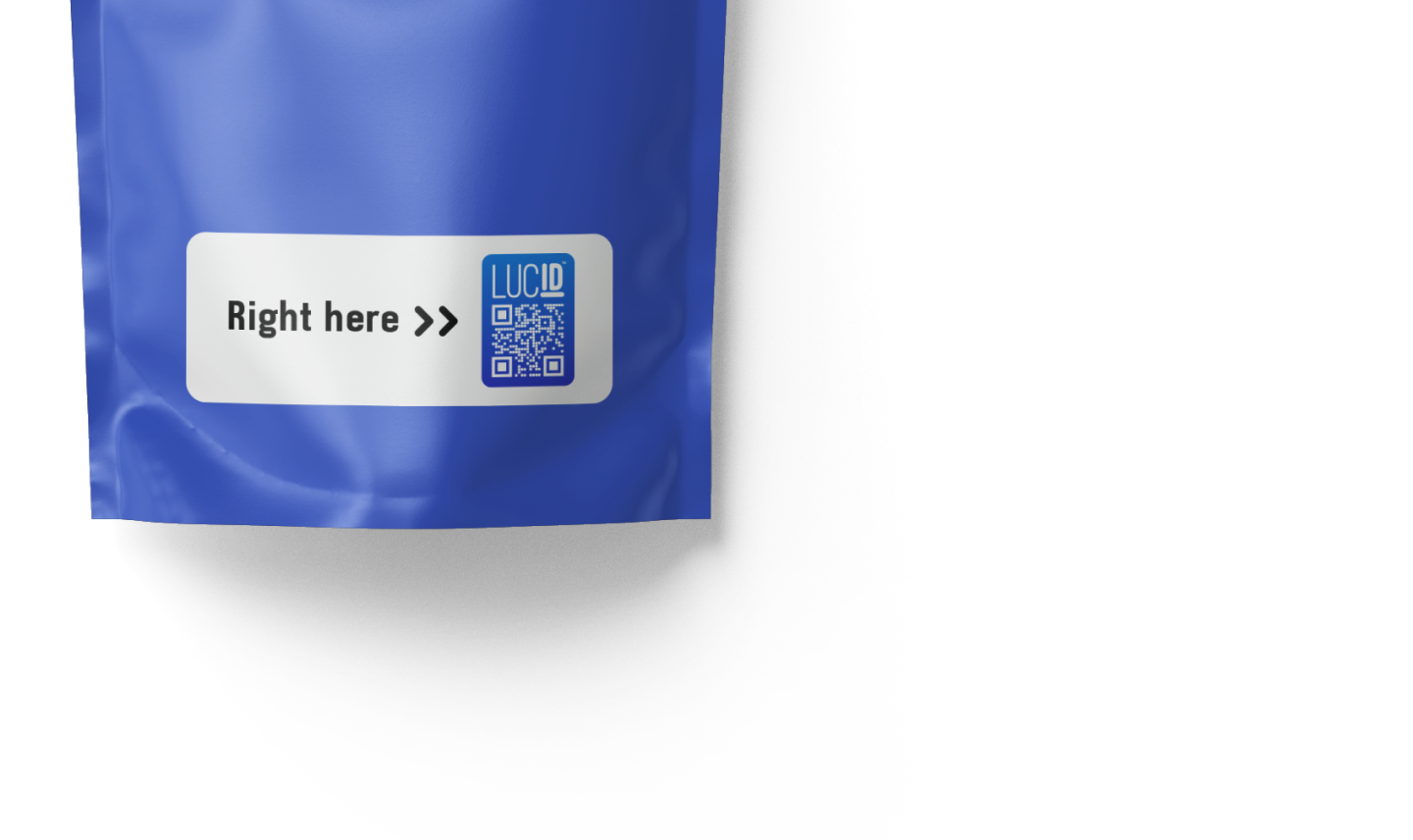
One platform to reduce costs, increase transparency and drive growth
LucidID saves you money and time. It makes your processes smarter. For licensed cannabis retailers that look to optimize inventory management, including cycle counting, to better manage working capital. Powered by the Lucid platform, it’s the industry’s most powerful cannabis supply chain management platform.
Who should be doing it:
Brands or Retailers?
Data points out that product ticketing should happen as early in the process as possible.
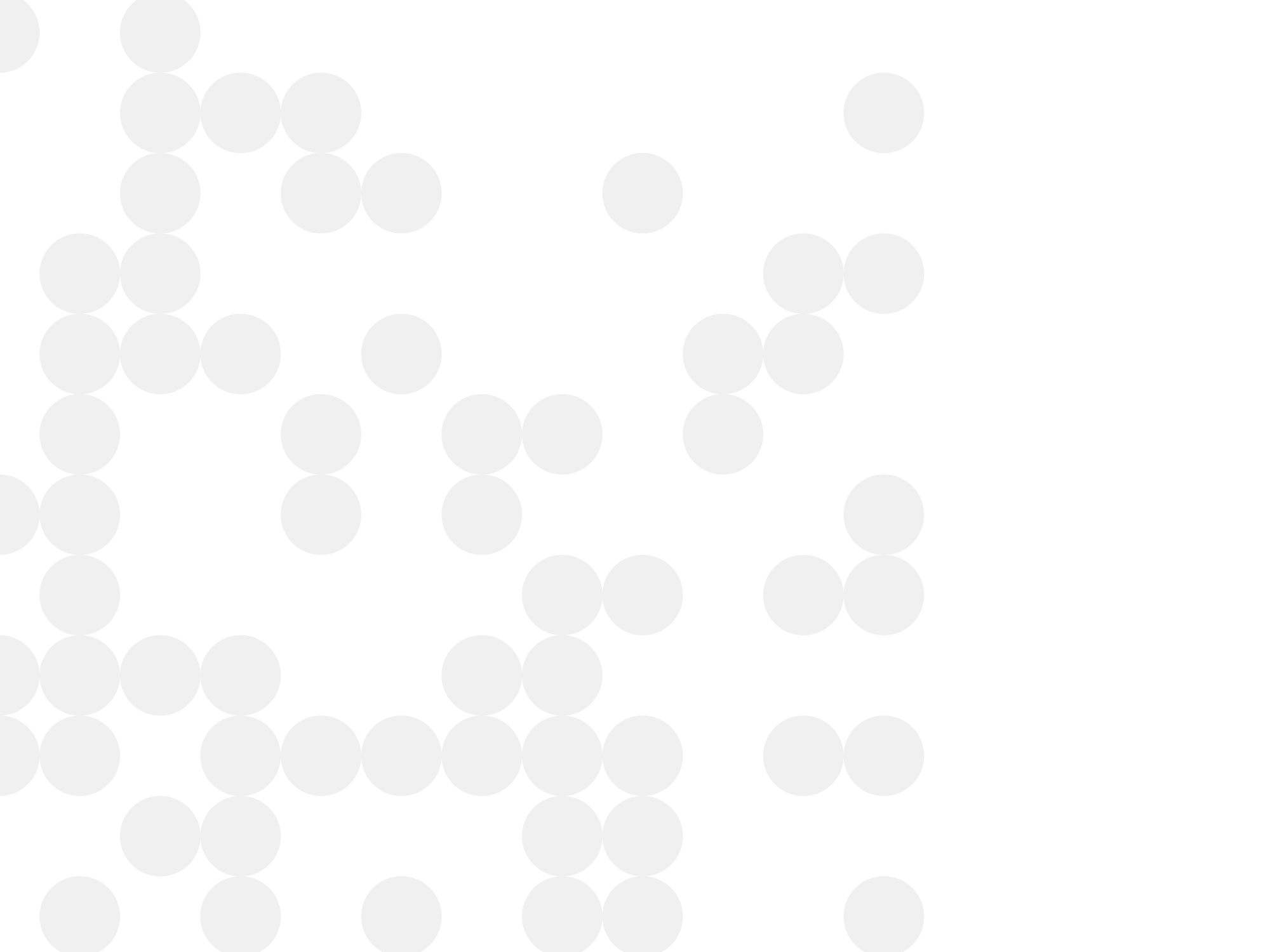
The Intelligent UPC of Cannabis Inventory Management
It’s not just faster and cheaper.
It’s smarter.
It saves your inventory team precious hours that they can invest in more meaningful work that creates value. Who doesn’t want to save between $7k-$20k/month per store!
The most effective solution to reduce truck-to-shelf time, increase product margins, reduce operational expenses and manual cannabis inventory tracking.
Drivers spend between 1-2 hours in each store, waiting for the unloading and storing process to be completed. That is a lot of time wasted.
With LucidID, time spent drops down to just 15 minutes!
Errors take so much time and energy. With LucidID, and no manual work related to data entry, there is one less thing to worry about.
Calculate your exact monthly savings!
We made a calculator that shows you exactly how much money you can save if you switch to LucidID, per period & per store.
It’s super easy to use, too.
Estimated Monthly Saving:
Estimated Yearly Saving:
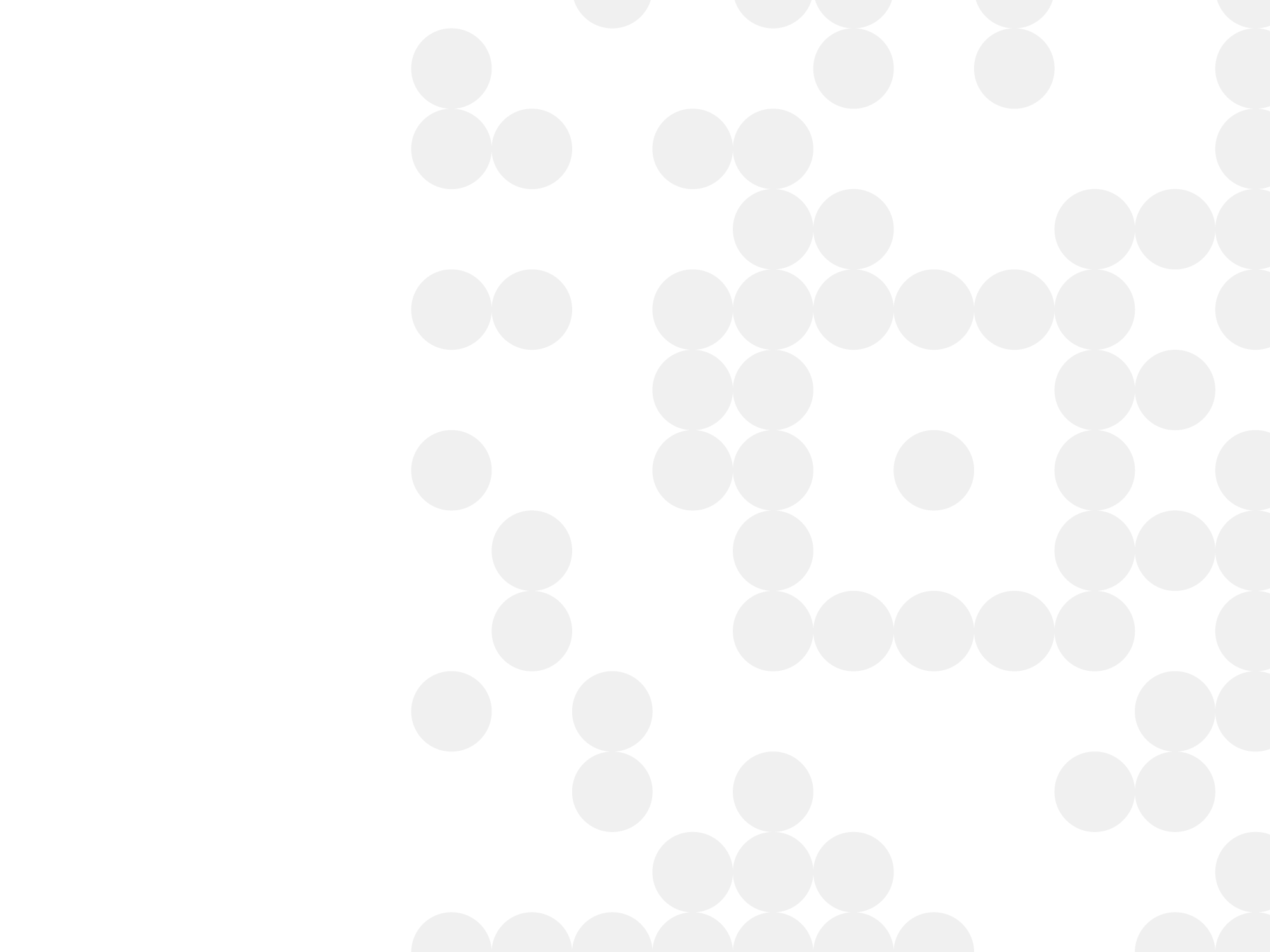
80% reduction in time
STANDARD STICKERING
10-15min
Product packaged
Compliance label added
Product placed into sellpack
Product stored
Order comes in
Package UID is identified via METRC
QR codes generated through the online editor
Print out QR codes on sticker sheets
Product pulled out of inventory
Sellpack reopened, packages are removed
Packages individually stickered with QR codes
Re-placed into sellpacks
WITH LucidID IMPLEMENTED
2-3min
Product is packaged
LucidID is applied to the product. No additional sticker is needed on the packaging, as LucidID is integrated on the compliance label through the brand’s normal printing process.
Product is scanned into sell packs
Product is stored and ready to be shipped to retail